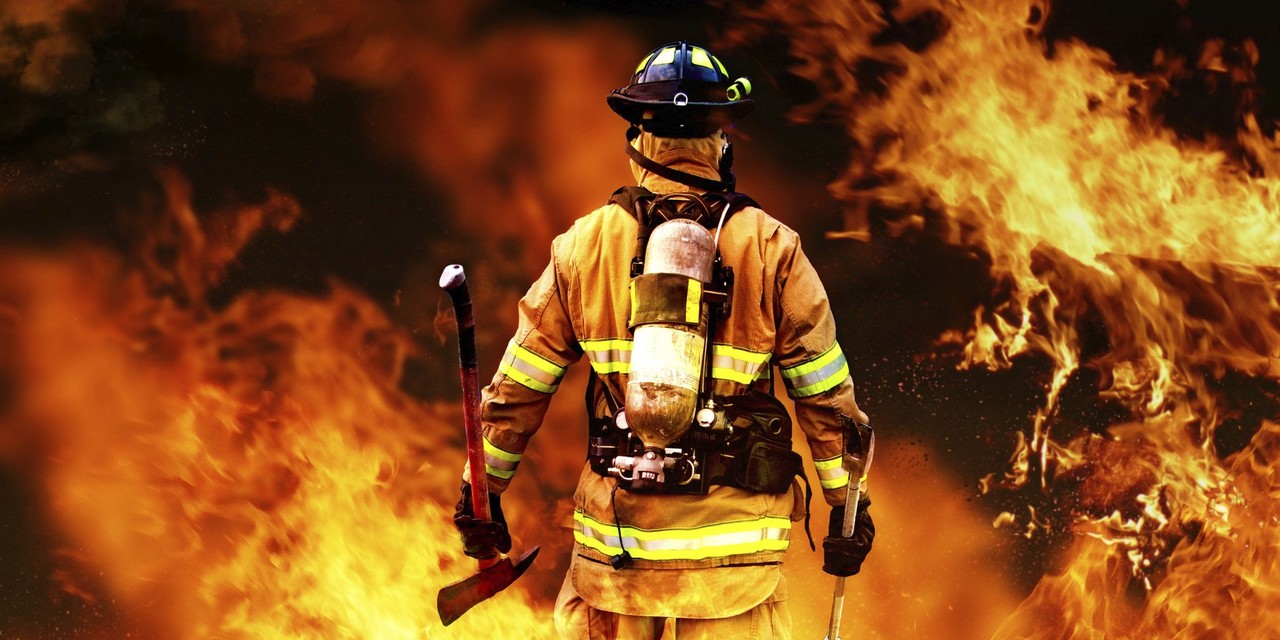
Existen dos tipos de empresas, las intensivas en maquinaria y las intensivas en personas. Si una fábrica incrementa al doble la cantidad de gente y la producción sube proporcionalmente, será intensiva en gente. Pero si para incrementar la producción se necesita incrementar la cantidad de maquinaria significativamente, entonces será intensiva en máquinas. Cuando este es el caso, entonces no solo la cantidad de producción dependerá de las maquinas, sino también la calidad y la seguridad serán consecuencia de la forma en que las maquinas son operadas y mantenidas. A mayor dependencia de las máquinas para la producción, mayor importancia estratégica tendrá el departamento de mantenimiento.
Muchas empresas ya reconocen este hecho, sin embargo, para la mayoría, el departamento de mantenimiento es solo una especie de departamento de bomberos interno que solo es requerido para ir a “apagar” incendios cuando la situación en producción así lo requiere.
En este último escenario, la gran mayoría del recurso asignado a tareas de mantenimiento se utiliza para tareas correctivas. Los equipos ya fallaron y es necesario regresarlos a su estado operacional a la brevedad. Los objetivos de producción de corto plazo son los que importan. No se mide el tiempo caído ni la eficiencia operativa, tampoco el costo incurrido en las tareas correctivas. Así, el departamento de mantenimiento se convierte en el eslabón débil de la empresa impidiendo que la organización pueda alcanzar estándares de desempeño elevados en productividad, calidad y servicio.
Sin una estrategia adecuada, la capacidad perdida por tiempos caídos y bajas eficiencias suele poner en confrontación a los líderes de producción y de mantenimiento, pues los primeros culparan a los segundos por su incapacidad para cumplir las metas de producción. En algunas ocasiones, la gerencia de planta reacciona haciendo que la función de mantenimiento reporte a la gerencia de producción. La lógica detrás de esta decisión es clara: Dejar al gerente de producción sin excusas para no cumplir sus metas. Ahora él puede organizar al grupo de mantenimiento como considere adecuado para lograr cumplir los objetivos.
A pesar de que esa decisión pueda parecer viable, raras veces funciona y en la mayoría de los casos solo hace que el problema se agrave. El énfasis en las tareas correctivas se intensifica, se abusa del tiempo extra entre el personal técnico, compras indiscriminadas de repuestos no siempre bien administrados y la subcontratación innecesaria de servicios técnicos externos que pueden prevenir el desarrollo del personal interno e inflan los costos de operación. El grupo de producción tenderá a tomar las decisiones que favorezcan los métricos propios: el cumplimiento al plan de producción, sin considerar el efecto en otros métricos sobre los cuales no se le exige en la misma medida, como los costos de mantenimiento, que por consecuencia suelen dispararse.
La función de mantenimiento es por su naturaleza, una función de ingeniería. Las plantas de clase mundial generan expectativas para este grupo por mucho más demandantes que las de solo reparar los equipos. En una organización moderna se espera que el grupo de mantenimiento:
1. Desarrolle programas de mantenimiento que eviten los paros repentinos, se espera que esos programas prevengan también problemas de calidad.
2. Que desarrolle planes que minimicen riesgos de seguridad en la interacción con la maquinaria
3. Que estos planes aseguren que la planta cumpla con regulaciones ambientales.
4. Que busquen optimizar el aprovechamiento de sus recursos tanto humanos como materiales.
Para cumplir las expectativas que se tienen, el grupo de mantenimiento deberá hacer uso de habilidades técnicas y humanas que busquen el desarrollo y aprovechamiento del personal técnico: técnicos e ingenieros y la colaboración con su principal cliente: el personal de producción.
Por el lado técnico, es importante establecer que el objeto de enfoque es la maquinaria, que si no recibe el mantenimiento adecuado y es operada propiamente se va a desempeñar a estándares inferiores. Cada máquina entonces deberá recibir un plan de mantenimiento hecho a la medida que considere su contexto de operación. Esto implicaría que maquinas idénticas pueden terminar con programas de mantenimiento distintos si su contexto de operación es diferente. Las tareas y la frecuencia de ejecución de cada una estarán orientadas a la prevención de fallas específicas. Estas tareas pueden ser para prevenir que una falla ocurra (tareas preventivas), o para detectar una falla que está por ocurrir y que ya está manifestándose en el equipo sin aun afectar el desempeño del mismo (tareas predictivas). Es vital que el personal técnico domine alguna metodología y herramientas de análisis de causa raíz y estas deberán ser aplicadas para determinar el conjunto de tareas necesarias para prevenir y/o detectar las fallas antes de que tengan un impacto en la disponibilidad del equipo o la calidad del producto. Estas tareas se enriquecerán las sugeridas por el fabricante. También deberán incluirse tareas de limpieza. Una maquina limpia siempre funcionará mejor que una que no lo este.
Una vez establecida la lista de tareas a realizar, se deberá determinar si la naturaleza de la tarea requiere que sea personal técnico el que tenga que realizarla. Para sorpresa de muchos, la mayoría de esas tareas puede ser llevada a cabo por personal que no tiene una carrera técnica. Estas son tareas de limpieza, lubricación e inspección que son muy efectivas para prevenir una gran cantidad de fallas o detectan algunas que están por ocurrir. Detectar una falla que esta por ocurrir permite a mantenimiento programar una tarea técnica que evite el paro repentino en un horario donde no afecte al plan de producción. Una tarea de mantenimiento programado siempre será menos costosa que una tarea no programada. Entonces es tiempo de establecer colaboraciones con los demás departamentos interesados, especialmente con el área de producción, ya que estas tareas de naturaleza no-técnica pueden ser llevadas a cabo por el mismo operador de la máquina (mantenimiento autónomo), enriqueciendo su trabajo, incrementando sus habilidades y conocimiento de la máquina y afectando positivamente la disponibilidad del equipo a la vez que se reducen los costos de mantenimiento. Este es el lado humano de la función de mantenimiento, ya que son los mismos técnicos los encargados de entrenar y asesorar a los operadores para que puedan realizar esta función de manera efectiva y sin poner en riesgo la seguridad del trabajador o de la máquina.
La aplicación rigurosa de los programas de mantenimiento (preventivo, predictivo y autónomo) por si mismas no garantizan que los objetivos de mantenimiento se cumplan. Es interesante ver como muchos gerentes de mantenimiento consideran como su métrico más importante el porcentaje de cumplimiento al programa de mantenimiento sin cuestionar la efectividad del mismo ni el costo incurrido en cumplirlo. Aun cumpliendo con el programa, puede ser que algunas fallas sigan presentándose a pesar de existir tareas destinadas a prevenirlas o puede ser que algunas tareas que ya son efectivas en la prevención de fallas puedan ser reemplazadas por otras tareas más económicas e igual de efectivas. Para aplicar el proceso de mejora a los estándares de mantenimiento aplicaremos el ciclo PDCA para determinar que ajustes al plan de mantenimiento o al diseño de la maquina deben hacerse. Esto será una actividad de equipo entre todos los interesados en el desempeño de la máquina.
La aplicación disciplinada de los estándares de mantenimiento y del ciclo de mejora necesariamente llevará a mejorar los métricos del departamento de mantenimiento. La calidad de su trabajo será mejor, los costos de mantenimiento se reducirán y los tiempos relevantes para ellos mejorarán, entre estos el tiempo medio para reparar y el tiempo medio entre fallas.
El departamento de mantenimiento, visto como una extensión de la función de ingeniería se podrá convertir así en un verdadero aliado estratégico para la empresa y un pilar de su ventaja competitiva.
Jorge Gabriel Martinez LizamaEntrepreneur, CEO at Gemba Productive Technologies LLC , industry 4.0 practitioner, Book Author, Founder & Global Director of ACADEMIA LEAN SIGMA SC, Operational Excellence Consultant.