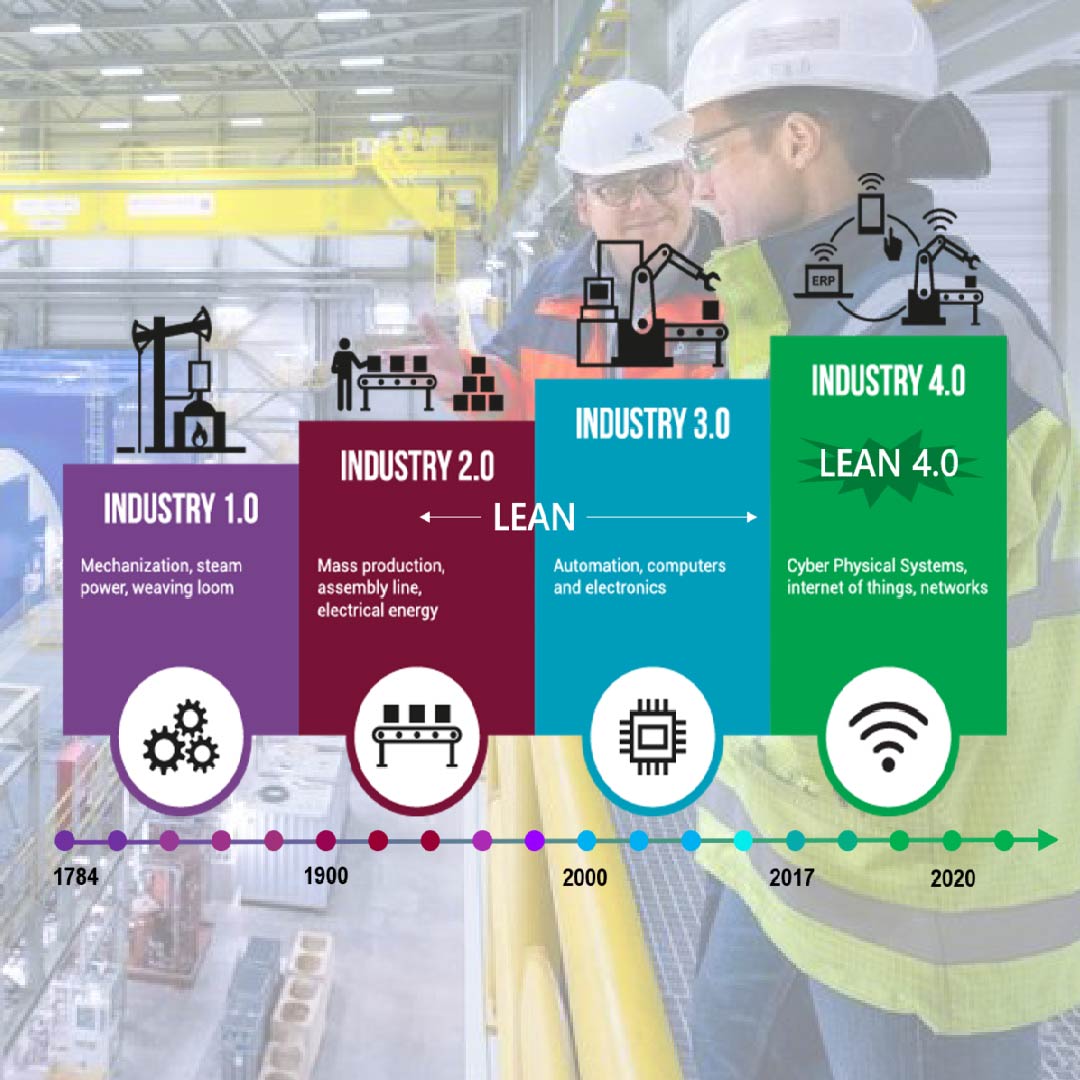
El termino comenzó a circular apenas durante los últimos 2 años y hace mucho sentido porque le da un nuevo matiz a las iniciativas de mejora continua basadas en el movimiento Lean Six Sigma. Me permitiré primero definir los dos términos que la componen: “Lean” y “4.0” para después explicar en qué consiste y porque apunta a ser un movimiento de gran impacto en los próximos años.
Lean surge del proceso de occidentalización del Sistema de Producción Toyota. Los principios y herramientas son los mismos solo que matizados para ser compatibles con el estilo gerencial occidental. El objetivo de Lean es elevar la competitividad de la organización enfocándose en crear valor para el cliente, reduciendo sistemáticamente los desperdicios en una dinámica conocida como Kaizen, recurriendo a la participación voluntaria de todos los trabajadores.
Por otro lado, la iniciativa Industria 4.0, obtiene su nombre al considerarse la 4ta revolución industrial. Aquí consideramos la incursión de nuevas tecnologías a los ambientes de producción a una tasa mucho más acelerada que en tiempos pasados. Tecnologías como “internet de las cosas”, “computación en la nube”, “inteligencia artificial” y “robots colaborativos” “data analytics” empiezan literalmente a invadir los ambientes de producción principalmente por dos razones: son muy accesibles en costo y realmente ayudan a adaptarse a los cada vez más frecuentes cambios en los patrones de demanda.
Lean 4.0 entonces es la combinación de ambos movimientos. “La mejora continua basada en la filosofía del Sistema de Producción Toyota ahora asistida con las tecnologías surgidas del movimiento Industria 4.0”. Y hay un propósito en esto, que las compañías puedan mejorar la forma en que mejoran. O dicho de forma, acelerar el ritmo de mejora.
Lean 4.0 no es una revolución de Lean. Es más bien, una evolución. De la misma forma que Lean evoluciona del movimiento de Control Total de la Calidad TQC. Lo que se desarrolla en uno, sirve como cimiento del otro. Se fortalecen los puntos débiles y se agregan elementos que lo hacen más robusto y efectivo.
Esta evolución era necesaria y eso era evidente. La efectividad de las iniciativas Lean en la mayoría de las compañías es bajísima, los resultados no son proporcionales al esfuerzo y todas experimentan problemas para sostener los logros en el largo plazo. Y esto es de esperarse si vemos que la mayoría trata de implementar Lean de la misma forma que lo hizo Toyota hace 50 años. Esto no tiene sentido porque el mercado ahora tiene requerimientos más exigentes y los ambientes de manufactura son mucho más complejos y regulados. Precisamente las razones por las que las nuevas tecnologías se han incorporado a los ambientes de producción.
Es interesante darse cuenta que son los líderes de mejora continua los que más se resisten al movimiento Lean 4.0, yo les llamo “puristas”. Los que deberían ser “agentes de cambio” se resisten a cambiar e intentar formas nuevas. La premisa es que primero deben hacerlo funcionar de la forma vieja para entenderlo y entonces usar tecnología para hacerlo eficiente. ¿Dónde está escrita esa regla? ¿Y qué tal que sea precisamente la forma vieja la causa de los fracasos? Cuando una iniciativa 5S’s o TPM no se sostienen, los de abajo le echan la culpa a los de arriba y viceversa. Y el ciclo se repite una y otra vez con cada intento que se haga. Nadie cuestiona si el enfoque de implementación fue el adecuado. Es más fácil culpar al otro, es más fácil decir: se sostuvo mientras yo estuve ahí.
Implementar Lean “a la vieja escuela” es en sí, una receta para el fracaso, porque esa fórmula fue escrita para una cultura oriental que fabricaba automóviles hace 50 años. Ahora, ni los automóviles son los mismos, ni somos orientales ni son los mismos tiempos. La evidencia de que ese método no funciona es abrumadora, solo hay que estar dispuestos a verla y a intentar formas nuevas de baja inversión y que prometan reforzar zonas débiles.
Sabemos que la disciplina es nuestro talón de Aquiles. ¿Qué tal si usamos tecnología para monitorear el cumplimiento al trabajo estándar para lideres?
Sabemos que Gemba es ahora más grande en extensión y que hace muy complicado estar presente todo el tiempo. ¿Qué tal si usamos tecnología para estar en Gemba aun sin estar en Gemba?
Sabemos que el propósito de Andón no es solo comunicar la situación de Gemba, sino asegurar que se toma la acción adecuada cuando es necesario. ¿Qué tal si usamos tecnología para que Gemba comunique inmediatamente a los interesados cuando hay un problema y también nos diga si ya se tomó acción e incluso si la acción fue efectiva?
¿O si usamos tecnología para recordar a la gente que tiene que realizar tareas de mantenimiento, guiarlas en el proceso y avisar a la gerencia si esto no está ocurriendo así?
¿O si usamos tecnología para asegurar que las acciones correctivas implementadas se sostienen adecuadamente y que están siendo efectivas?
El uso de tecnología de baja inversión para apoyar la implementación de LEAN es perfectamente compatible con los principios del Sistema de Producción Toyota. Reconocer que la gente no es perfecta y que necesitamos dispositivos para hacer evidente que algo no se está haciendo bien. En aquellos tiempos los dispositivos eras fixturas pokayoke para prevenir errores, luces de andón para indicar situación, tarjetas de kanban para comunicar requerimientos y pizarrones visuales para comunicar desempeño. Hoy los dispositivos son: computación en la nube, aplicaciones móviles, inteligencia artificial y realidad aumentada utilizados para los mismos propósitos. Las formas pueden ser diferentes, pero los principios son los mismos. Y las nuevas formas son mejores si consideramos el efecto en el verdadero objetivo, construir una organización más competitiva.
Si quieres saber un poco más de Lean 4.0 y cómo empezar a dar primeros pasos en este nuevo mundo, mándame un correo a Jorge.martinez@academialeansigma.com
Jorge Martínez.